Fabrication d'un stabilisateur moulé plein :
Intérêt : Obtenir la rigidité et la robustesse d'un stab plein en polystyrène et la précision d'une pièce moulée. Il n'est plus nécessaire de faire de sandwich mais une peau carbone est nécessaire pour résister à l'écrasement. Pour un planeur peu martyrisé, une peau en verre peu suffire.
Pas besoin de découper des noyaux ajustés, on peut faire des stab elliptiques sans problème en déformant des plaques de polystyrène d'épaisseur constante.

Comme pour tout moulage, on commence par peindre les moules ! Une fois la peinture sèche, je la raye là où l'articulation sera pour ne pas avoir à mesurer ou tomber a coté du tissu d'arrachage. Sa position est donc marquée.
On pose ensuite le tissu de surface (verre 25gr ou 50gr/m²). Cette opération est facultative mais permet d'obtenir un très bon aspect de la pièce. Cependant, elle coûte de 10 à 15 gr de plus sur le stab fini. Pour cet essai, le tissu de surface est un 50gr/m². Il faut vraiment minimiser la quantité de résine, quitte à pomper l'excédent avec du papier essuie-tout. On laisse sécher.
La prochaine étape consistera à poser le carbone et polystyrène : pour cela, on découpe des plaques de polystyrène de 2 ou 3mm plus épaisses qu'un 1/2 stab. Mes plaques font 7mm environ. Il faut donc 2 plaques entières ou 4 quarts de stab en tapant dans les chutes de polystyrène.
Ca part : on pose le tissu d'arrachage a l'extrados pour l'articulation, puis le carbone 93gr/m² (en tirant la résine comme toujours !) et enfin on met en place les plaques de poly.
Et hop, sous vide ! Je règle ma pompe pour tirer fort le vide (de 700 à 900gr) pour bien écraser le polystyrène dans les courbes du stab. On laisse sécher…

Pour gagner un peu de temps, on peu enlever le plus gros du polystyrène en plus avec un fil chaud. Attention à surélever l'arc d'un mm environ avec des cales en balsa pour compenser le rayonnement du fil. On protége ensuite le plan de joint et on fini d'araser les 2 coquilles à la cale à poncer. Objectif, finir à fleur du plan. Ensuite on arase le carbone qui dépasse.
On peut ensuite préparer les inserts : fourreaux, insert en microballon pour 1 ou 2 pions de centrage, vis… J'en profite pour fermer le champ du volet avant de le découper en créant 2 fentes en vis-à-vis qui selon remplies de microballon.
Il faut également gratter le polystyrène le long du bord d'attaque sur une bande de 2mm environ. Remplie de microballon, cela constituera un bord bien rigide.
L'heure est venue de fermer le moule : Au choix, soit 100% microballon, soit 50% microballon et 50% colle PU. Pour avoir essayé les 2, je pense qu'il vaut mieux la seconde méthode, moins lourde. Mais attention, la PU a besoin d'air pour sécher rapidement et dans un moule fermé, il n'y en a pas beaucoup. Il faudra donc surveiller le temps de séchage.
Un coup de seringue remplie de microballon tout le long des bords d'attaque et de fuite, autour du fourreau et des inserts… puis PU, éventuellement diluée au cœur du stab… et on ferme.
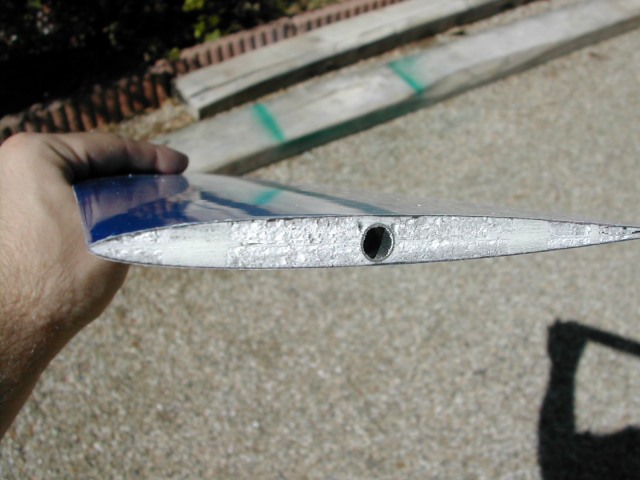
Le stab obtenu est extrêmement résistant grâce a la peau carbone et au polystyrène haute densité (classe sol) employé. Il subsiste un petit écart entre les 2 coquilles, sans importance. Ce stab a été collé a 100% au microballon et la PU aurait été avantageusement utilisée !
Au résultat, le stab pèse 94gr, soit environ 20gr de plus qu'un stab creux "crounchable", mais cette masse peut être améliorée :
- avec du poly moins dense
- en supprimant le tissu de surface (on pose le carbone et dès que la résine poisse, on repasse un léger film de résine et on pose le poly)
- en collant les 2 coquilles à la PU+microballon
Mon premier essai, avec une peau carbone (sans tissu de surface) et du poly classe sol, fermé à la PU pesait 80gr…mais avait quelques porosité en surface. Le second est un peu plus lourd, le troisième sera parfait !
Bien sur, cette technique peut être employé sur des ailes, notamment en 60" ! Finis les superbes planeur moulés trop fragiles qui explosent lorsqu'un impact.
Au niveau coût, avec un tissu de surface, on peut se permettre de faire la peau carbone avec plusieurs chutes raboutée. De toute façon, ce sera quasi aussi cher que des planches de balsa plumes…
Au niveau temps, c'est beaucoup plus court, il n'y a qu'une seule mise sous vide (contre 2 pour le creux). Le matin, on peint+pose du tissu de surface, le soir carbone+poly. Lendemain matin on arase, on ponce et on ferme à midi.
Facile non ?
C'est un article que j'avais posté sur Planet-soaring il y a quelques années...